The Industrial Process Optimization Journey:
History, Benefits, and Steps for Success
Introduction to Industrial Process Optimization
The ever-evolving landscape of the industrial sector demands continuous improvement and innovation to remain competitive and efficient. One of the critical aspects of ensuring success in this dynamic environment is the optimization of industrial processes. In this guide, we will embark on an insightful journey through the history of industrial process optimization, its numerous benefits, and the essential steps required for achieving success in this crucial area.
As we begin our exploration, it is essential to understand the fundamentals of industrial process optimization and its significance in today’s modern industrial landscape. In the following sections, we will provide a brief overview of industrial process optimization, discuss its importance in the contemporary industrial setting, and delve into the history and evolution of optimization techniques and technologies.
JOIN US AS WE EXPLORE THE FOLLOWING TOPICS:
- Brief Overview of Industrial Process Optimization
- Importance of Optimization in the Modern Industrial Landscape
- History of Industrial Process Optimization
- Evolution to Digital Process Optimization
- The Next Step in Industrial Process Optimization: A Total Systems Approach to Performance Monitoring
- Steps of the Industrial Process Optimization Journey
- Harnessing Total Systems Approach and Real-World Applications
- Embracing the Future of Industrial Process Optimization
Brief Overview of Industrial Process Optimization
Industrial process optimization refers to the systematic approach of analyzing, evaluating, and enhancing various processes within the manufacturing and production sectors. The primary objective is to maximize productivity, minimize waste, improve product quality, and optimize resource utilization. Throughout history, various methodologies and technologies have emerged, enabling organizations to streamline their operations and achieve superior performance.
Importance of Optimization in the Modern Industrial Landscape
In today’s competitive global market, the ability to adapt and optimize industrial processes has become more vital than ever. The modern industrial landscape is characterized by rapid technological advancements, increasing complexity, and growing environmental concerns. Consequently, organizations must constantly strive for process optimization to maintain their competitive edge, meet customer expectations, and comply with regulatory requirements. By embracing the principles of industrial process optimization, businesses can unlock untold efficiencies, reduce costs, and enhance overall performance, ensuring long-term success in a constantly evolving landscape.
Let’s delve deeper into the fascinating world of industrial process optimization, exploring its rich history, the myriad benefits it offers, and the essential steps to successfully implementing optimization strategies in your organization.
History of Industrial Process Optimization
The evolution of industrial process optimization has significantly shaped the landscape of organizational and manufacturing practices throughout history. Beginning with foundational approaches like Taylorism and scientific management, the journey progressed through the development of statistical process control and total quality management. As technology advanced, it revolutionized the field, introducing innovations such as computer-aided manufacturing, automation, robotics, artificial intelligence, and machine learning. This section explores the early attempts at process optimization and the transformative impact of technology, highlighting the ongoing quest for enhanced productivity, efficiency, and quality in the industrial sector.
Early Attempts at Process Optimization
Industrial process optimization has played a pivotal role in the growth and development of organizations since the inception of the industrial revolution. Early efforts aimed to enhance efficiency, quality, and productivity by employing scientific principles, statistical methods, and management practices. Three prominent approaches emerged during this era:
Tracing back to the late 19th and early 20th centuries, the origins of process optimization begin with the introduction of Taylorism, also known as scientific management. Frederick Winslow Taylor developed this management approach to systematically analyze and optimize work processes, ultimately boosting efficiency and productivity. Taylor’s method involved breaking down tasks into basic components, determining the most efficient way to perform each, and training workers to execute those tasks in a standardized manner.
Taylor’s work laid the foundation for numerous future process optimization techniques. His scientific management principles emphasized efficiency, standardization, and data-driven decision-making. While Taylorism continues to influence modern management practices, it has faced criticism for prioritizing worker efficiency over worker well-being.
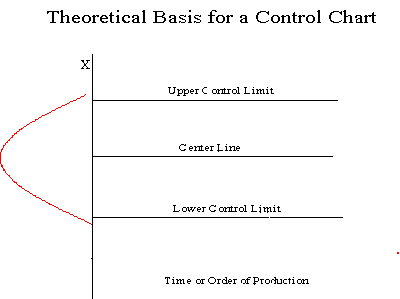
Building upon Taylor’s foundation, statistical process control (SPC) emerged in the 1920s and 1930s. Walter A. Shewhart developed SPC as a quality control method that employs statistical techniques to monitor and manage production processes. By gathering and analyzing data on process variation, SPC enables organizations to pinpoint inefficiencies’ root causes and implement improvements accordingly.
A fundamental SPC tool is the control chart, which visually displays process performance and indicates when a process is in or out of control. This allows organizations to detect trends and patterns in their processes, promoting continuous improvement and reducing the likelihood of defects. SPC has become a critical component of modern quality management systems and is extensively used across various industries.
In the 1950s, Total Quality Management (TQM) emerged as an all-encompassing approach to quality improvement, drawing inspiration from the work of W. Edwards Deming and Joseph M. Juran. TQM is an organization-wide philosophy that prioritizes continuous improvement, customer focus, and employee involvement in the quest for quality excellence.
TQM incorporates the principles of Taylorism and the techniques of SPC into a holistic framework. Key elements of TQM include fostering a customer-centric culture, utilizing cross-functional teams to identify and address problems, and applying statistical methods for process analysis and enhancement. TQM has been embraced by numerous organizations globally, including Ford Motor Company, Phillips Semiconductor, SGL Carbon, Motorola, and Toyota Motor Company. The result has been significant improvements in product and service quality, customer satisfaction, and overall organizational performance.
The Role of Technology in Process Optimization
Technology has played a transformative role in process optimization, profoundly impacting the evolution of industrial and organizational practices. Initial attempts at process optimization witnessed the emergence of computer-aided manufacturing, the rise of automation and robotics, and the integration of artificial intelligence and machine learning. These technological advancements have revolutionized how organizations approach productivity, efficiency, and quality:
The advent of computer-aided manufacturing (CAM) in the 1940s and 1950s marked a significant milestone in the integration of technology with process optimization. CAM involves the use of computer software and hardware to plan, control, and manage various manufacturing processes. By automating the creation of detailed production instructions, CAM enables faster and more accurate production, streamlining the design-to-manufacturing process.
CAM works in conjunction with computer-aided design (CAD) software, allowing for seamless integration between product design and production. This has led to reduced lead times, improved product quality, and increased manufacturing efficiency. The rise of CAM has played a pivotal role in the evolution of modern manufacturing, shaping the way organizations leverage technology to optimize production processes.
Automation and robotics have had a profound impact on process optimization since their emergence in the 20th century. Automation involves the use of machines and technology to perform tasks with minimal human intervention, while robotics refers to the design, construction, and operation of robots for various applications.
The integration of automation and robotics in manufacturing and other industries has greatly improved efficiency, productivity, and safety. By automating repetitive and labor-intensive tasks, organizations can achieve higher levels of precision and consistency, reducing the potential for human error. Additionally, the use of robotics has allowed for the execution of tasks in hazardous or inaccessible environments, improving worker safety and overall process effectiveness.
The rise of artificial intelligence (AI) and machine learning has further revolutionized process optimization, expanding the capabilities of existing technologies and enabling new levels of data-driven decision-making. AI refers to the development of computer systems capable of performing tasks that typically require human intelligence, while machine learning is a subset of AI that focuses on the ability of computers to learn and improve from experience.
The integration of AI and machine learning into process optimization has led to significant advancements in areas such as predictive maintenance, quality control, and supply chain management. By analyzing vast amounts of data, AI-powered systems can identify patterns and trends, enabling organizations to make proactive decisions, reduce downtime, and optimize resource allocation. Furthermore, machine learning algorithms can continuously adapt and improve, driving ongoing process enhancements and innovations.
Technology has played a transformative role in the history of industrial process optimization, shaping the way organizations approach efficiency, productivity, and quality. The rise of computer-aided manufacturing, the emergence of automation and robotics, and the integration of artificial intelligence and machine learning have paved the way for new levels of optimization, enabling organizations to harness the full potential of technological advancements to achieve their goals.
Evolution to Digital Process Optimization
The industrial process optimization landscape has undergone a significant transformation with the advent of Industry 4.0, moving from traditional methods to embracing digital process optimization. This shift integrates cutting-edge technologies revolutionizing process optimization and enabling unparalleled levels of connectivity, efficiency, and innovation.
As technological capabilities continue to evolve, new digital process optimization tools emerge to support organizations in achieving increased efficiency, productivity, and innovation. This section delves into the digital transformation of process optimization, emphasizing the influence of Industry 4.0 and the emergence of digital process optimization tools in driving continuous improvement and success within the industrial sector.
The Impact of Industry 4.0
Industry 4.0 signifies a paradigm shift from traditional to digital process optimization, marked by the incorporation of digital technologies like the Industrial Internet of Things (IIoT), Big Data and advanced analytics, digital twins, and simulation. These technologies have radically changed how organizations approach process optimization, unlocking unprecedented levels of connectivity, efficiency, and innovation.
Harnessing Industry 4.0 Technologies
for Process Optimization
Industrial Internet of Things (IIoT):- Network of interconnected devices, sensors, and machines
- Real-time data collection and exchange
- Enhanced operational efficiency and decision-making
- Implementation of predictive maintenance strategies
- Analysis of vast amounts of data from connected devices
- Identification of patterns, trends, and anomalies
- Informed decision-making and process optimization
- Discovery of new growth and innovation opportunities
- Virtual representations of processes, products, or systems
- Prediction of process performance and identification of improvements
- Data-driven decision-making and risk mitigation
- Reduced need for physical testing
Industrial Internet of Things (IIoT)
As a core component of Industry 4.0, the IIoT is a network of interconnected devices, sensors, and machines that collect and exchange real-time data. This connectivity allows organizations to monitor, control, and optimize their processes with remarkable precision and speed. Facilitating seamless communication and data sharing across the entire value chain, the IIoT enables more effective resource allocation, improved operational efficiency, and better decision-making. Furthermore, the IIoT has made predictive maintenance strategies possible, reducing equipment downtime and maintenance costs.
Big Data and Advanced Analytics
Industry 4.0 has led to an exponential increase in data generated from connected devices, machines, and systems, creating the vast potential for driving process optimization through advanced analytics. Employing sophisticated techniques like machine learning and artificial intelligence, advanced analytics processes and analyzes Big Data to derive actionable insights. By examining enormous volumes of data, organizations can identify previously undetectable patterns, trends, and anomalies, enabling informed decision-making, process optimization, and the discovery of new growth and innovation opportunities.
Digital Twins and Simulation
Digital twins and simulation play a vital role in Industry 4.0, allowing organizations to create virtual representations of their processes, products, or systems. Digital twins are digital replicas of physical assets, while simulation uses computer models to test and analyze different scenarios. Integrating digital twins and simulation in process optimization allows organizations to predict process performance and identify potential improvements without the need for costly and time-consuming physical testing. Through analyzing various scenarios and outcomes, organizations can make data-driven decisions to optimize processes and mitigate risks.
The Rise of Digital Process Optimization Tools
The evolution of digital process optimization tools has been instrumental in the transition from traditional industrial process optimization to digital process optimization. As technology progresses, a new generation of tools has surfaced to aid organizations in their pursuit of efficiency, productivity, and innovation. Notable advancements in this domain include advanced process control software, industrial optimization algorithms, and cloud-based optimization platforms.
Key Components of Digital Process
Optimization Tools
Advanced Process Control Software:- Monitors, analyzes, and optimizes complex industrial processes
- Utilizes algorithms, real-time data, and predictive modeling
- Incorporates artificial intelligence (AI) and machine learning techniques
- Drives continuous improvement and innovation
- Leverages mathematical models and computational techniques
- Identifies optimal solutions for complex industrial problems
- Supports decision-making and process improvement
- Adapts and improves over time with machine learning and AI
- Provides scalable and flexible optimization solutions
- Offers access to advanced analytics, simulation tools, and optimization algorithms
- Facilitates collaboration and data sharing
- Accelerates the transition to digital process optimization
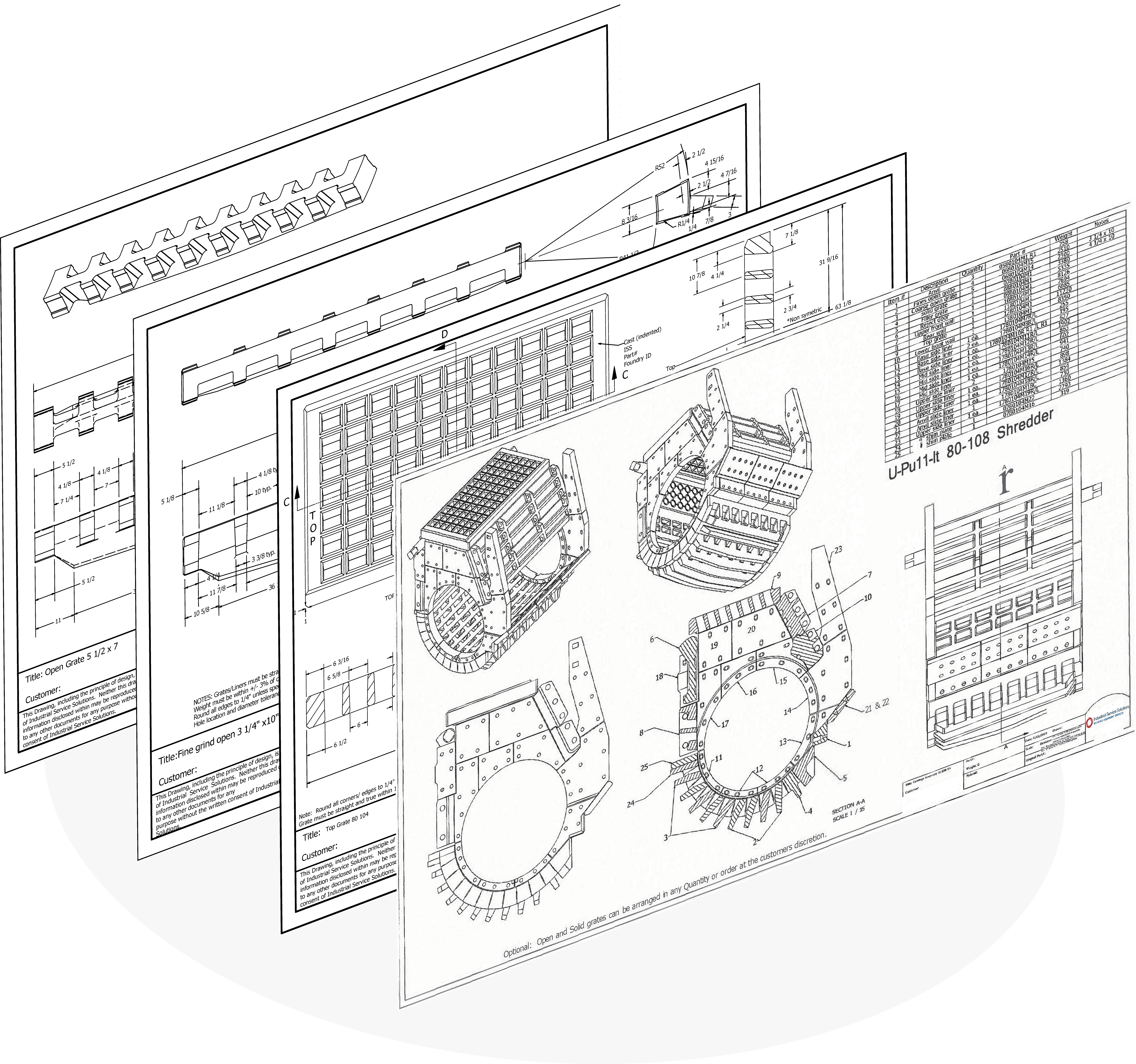
Advanced Process Control Software
Advanced process control (APC) software is a significant development in digital process optimization tools. Utilizing sophisticated algorithms, real-time data, and predictive modeling, APC software monitors, analyzes, and optimizes complex industrial processes. By continuously adjusting process variables and maintaining optimal conditions, APC software enables organizations to achieve higher levels of efficiency, product quality, and overall process performance.
APC software often incorporates artificial intelligence (AI) and machine learning techniques, allowing it to learn from historical data and make informed predictions about future performance. This enables organizations to proactively address potential issues and make data-driven decisions to optimize their processes. The integration of advanced process control software has been transformative for many industries, driving continuous improvement and innovation.
Industrial Optimization Algorithms
Industrial optimization algorithms are another key component of digital process optimization tools. These algorithms leverage mathematical models and advanced computational techniques to identify optimal solutions for complex industrial problems. By analyzing vast amounts of data and considering multiple variables, optimization algorithms can support decision-making and process improvement in areas such as production planning, scheduling, and resource allocation.
The use of optimization algorithms has become increasingly widespread as computational power has grown, enabling organizations to tackle previously intractable problems. Machine learning and AI techniques have further enhanced the capabilities of optimization algorithms, allowing them to adapt and improve over time. As a result, industrial optimization algorithms have become an indispensable tool for modern organizations seeking to drive process efficiency and innovation.
Cloud-Based Optimization Platforms
The rise of cloud computing has led to the development of cloud-based optimization platforms, which offer organizations a scalable and flexible solution for process optimization. These platforms provide access to advanced analytics, simulation tools, and optimization algorithms through a centralized, web-based interface. By leveraging cloud infrastructure, organizations can easily scale their optimization efforts, accommodate fluctuating demand, and reduce the need for costly on-site hardware.
Cloud-based optimization platforms also facilitate collaboration and data sharing across teams and locations, enabling organizations to harness the collective knowledge and expertise of their workforce. The widespread adoption of cloud-based optimization platforms has greatly accelerated the transition from traditional industrial process optimization to digital process optimization, providing organizations with powerful tools to achieve their goals.
The emergence of digital process optimization tools, including advanced process control software, industrial optimization algorithms, and cloud-based optimization platforms, has played a pivotal role in the evolution from industrial process optimization to digital process optimization. These tools have transformed the way organizations approach efficiency, productivity, and innovation, enabling them to harness the full potential of technology to optimize their processes and drive continuous improvement.
The Next Step in Industrial Process Optimization: A Total Systems Approach to Performance Monitoring
As the need for a more holistic approach to performance monitoring grows, the limitations of traditional remote condition monitoring in industrial processes have become increasingly apparent. These methods, which focus on individual components or equipment, depend on reactive maintenance and often lack advanced data analytics capabilities. In response, true performance monitoring has emerged within a total systems approach, revolutionizing industrial process optimization by offering a comprehensive, proactive, and data-driven solution for managing and enhancing overall system performance.
The Limitations of Traditional Remote Condition Monitoring
Traditional remote condition monitoring has been paramount for detecting and diagnosing equipment issues in industrial processes. However, it presents certain limitations when compared to a total systems approach to performance monitoring, which is widely considered the next step in industrial process optimization. These limitations include:
- Focusing on individual components or equipment rather than the entire system
- Relying on reactive maintenance
- Limited advanced data analytics capabilities
Traditional remote condition monitoring typically concentrates on individual components or equipment instead of the entire system. This can result in a narrow understanding of overall process performance and potential inefficiencies that might be hidden when analyzing components in isolation. In contrast, a total systems approach accounts for the interactions among all elements within the process, yielding a more comprehensive view of performance and optimization opportunities.
One significant drawback of traditional remote condition monitoring is its reliance on reactive maintenance, addressing issues only after they arise. This can cause unplanned downtime and increased maintenance costs. Conversely, a total systems approach to performance monitoring emphasizes predictive and proactive maintenance strategies, enabling organizations to identify potential problems before they escalate and optimize their maintenance schedules.
Moreover, traditional remote condition monitoring frequently lacks advanced data analytics capabilities, limiting its potential to provide actionable insights for process improvement. However, a total systems approach utilizes advanced analytics and machine learning techniques to identify patterns and trends, facilitating more informed decision-making and the development of targeted optimization strategies.
A total systems approach to performance monitoring surpasses the limitations of traditional remote condition monitoring by offering a holistic view of process performance, fostering predictive maintenance, and leveraging advanced analytics for informed decision-making. As a result, it marks the next stage in industrial process optimization.
The Emergence of True Performance Monitoring
The development of true performance monitoring within a total systems approach signifies a major breakthrough in industrial process optimization. It provides a more comprehensive and proactive solution for managing and improving the overall performance of industrial systems, transcending the limitations of traditional remote condition monitoring.
Key aspects of true performance monitoring include:
- Real-time analysis of data from all aspects of the system
- Emphasis on predictive and proactive maintenance
- Promotion of continuous improvement and innovation within the organization
True performance monitoring involves real-time analysis of data from all aspects of the system, encompassing equipment, processes, and interactions between components. This comprehensive approach allows organizations to identify inefficiencies, bottlenecks, and improvement opportunities that might not be discernible when focusing on individual components. As a result, it establishes a strong foundation for data-driven decision-making and the implementation of targeted optimization strategies.
In addition to offering a more extensive view of system performance, true performance monitoring emphasizes predictive and proactive maintenance. Utilizing advanced analytics, machine learning, and Industrial Internet of Things (IIoT) technologies, organizations can detect potential issues before they worsen, minimizing unplanned downtime and optimizing maintenance schedules. This proactive strategy leads to more reliable and efficient operations, ultimately boosting overall productivity and profitability.
Furthermore, true performance monitoring fosters continuous improvement and innovation within the organization. By cultivating a culture of ongoing optimization and adopting the latest advancements in performance monitoring technologies, organizations can outpace the competition and adapt more effectively to evolving market demands.
The emergence of true performance monitoring as part of a total systems approach marks a pivotal development in industrial process optimization. By providing a comprehensive, data-driven, and proactive solution for managing system performance, true performance monitoring paves the way for increased efficiency, reliability, and competitiveness in the industry.
The Role of Industrial Service Solutions and the Spectare® Intelligent Platform
Industrial Service Solutions and our Spectare® Intelligent Platform play a pivotal role in advancing industrial process optimization by implementing a total systems approach to performance monitoring. The Spectare® Process Optimization Condition Monitoring solution harnesses the power of real-time monitoring and analytics to prevent downtime, anticipate failures, and remotely track the performance of any asset or equipment within a facility. This innovative platform transforms real-time data into actionable insights, empowering organizations to make faster and smarter decisions for improved operational efficiency.
Key features of the Spectare® Intelligent Platform include:
- Real-time data collection for informed decision-making
- Data-driven AI algorithms and machine learning for predictive analytics
- High-resolution data storage for diagnostics and troubleshooting
- Secure cloud-based data storage for easy access
- Comprehensive customer dashboard for asset management
- Timely alerts and notifications for proactive interventions
- Usage insights for cost optimization and asset upgrades
- Remote support from expert engineers and technicians
- Predictive maintenance based on real-time and historical data
- Failure prediction through AI-driven anomaly detection
- Rapid response field service dispatching
- Spare parts management through AI-powered forecasting
- Seamless service history management for record-keeping
- Asset location tracking and optional GPS for mobile machines
By integrating these features, the Spectare® Intelligent Platform offers a comprehensive and proactive solution for performance monitoring, driving increased efficiency, reliability, and competitiveness in the industry. As a result, Industrial Service Solutions and the Spectare® Intelligent Platform play a significant role in realizing the full potential of a total systems approach to industrial process optimization.
Steps of the Industrial Process Optimization Journey
Industrial process optimization is an important factor for organizations seeking to improve efficiency, reduce waste, enhance product quality, and achieve greater environmental sustainability. By leveraging advanced technologies and data-driven methodologies, businesses can streamline their operations and remain competitive in an ever-evolving market landscape. This section outlines a six-step approach to effectively optimizing your industrial processes, from identifying goals and objectives to sustaining and refining the optimization process over time.
STEP 1:
Identifying optimization goals and objectives
The optimization journey begins by pinpointing the goals and objectives your organization aims to achieve. Consider the following:
- Increased efficiency
- Waste reduction
- Improved product quality
- Heightened environmental sustainability
By clearly defining these objectives, you can concentrate your optimization efforts and ensure alignment with your organization’s overall strategic vision.
STEP 2:
Assessing current processes and performance metrics
Subsequently, you must evaluate your existing processes and performance metrics to establish a baseline for improvement. This involves:
- Conducting a thorough analysis of your current operations
- Pinpointing areas for improvement
- Determining the key performance indicators (KPIs) that will help measure the success of your optimization endeavors
By completing these tasks, you can effectively track the progress and success of your optimization efforts.
STEP 3:
Gathering and analyzing data for process improvement
With a solid understanding of your current processes and performance, you can now collect and analyze data to drive process improvement. This may entail:
- Gathering historical data
- Performing real-time monitoring
- Utilizing advanced analytics tools to reveal trends, patterns, and potential areas for enhancement
Leveraging data enables you to make informed decisions about which optimization strategies and technologies to employ.
STEP 4:
Implementing optimization strategies and technologies
Guided by a data-driven approach, you can begin to introduce optimization strategies and technologies to enhance your processes. Some essential methods and tools to consider include:
- Continuous Improvement Methods: Techniques like Lean and Six Sigma can help streamline processes, eradicate waste, and boost efficiency. Applying these methodologies cultivates a culture of continuous improvement within your organization.
- Automation and Robotics Integration: Incorporating automation and robotics into your operations can substantially increase productivity, elevate product quality, and decrease human error. This may involve adopting automated assembly lines, robotic material handling systems, or automatic guided vehicles (AGVs).
- Advanced Process Control and Monitoring: Utilizing advanced process control software, IIoT, and real-time monitoring systems can optimize your processes by offering performance insights, detecting potential issues, and facilitating proactive adjustments.
By adopting these strategies and technologies, you can significantly enhance your organization’s performance and drive sustainable growth in the long term.
STEP 5:
Monitoring and evaluating the impact of optimization efforts
After implementing optimization strategies and technologies, it is essential to monitor and evaluate their impact. This includes:
- Tracking KPIs
- Scrutinizing data
- Measuring the results of your efforts against your initial goals and objectives
Continuous monitoring of your optimization initiatives ensures they deliver the desired outcomes and allows for necessary adjustments to maximize effectiveness.
STEP 6:
Sustaining and refining the optimization process over time
Lastly, it is crucial to maintain and refine your optimization process over time. This entails:
- Regularly reviewing your goals and objectives
- Monitoring performance metrics
- Making ongoing adjustments to your optimization strategies and technologies as required
By persistently refining your processes and staying current with the latest optimization tools, you can ensure that your organization remains at the cutting edge of industry best practices and maintains a competitive advantage in the market.
Harnessing Total Systems Approach and Real-World Applications
A total systems approach to performance monitoring, along with Industrial Service Solutions’ Spectare® Intelligent Platform, has advanced industrial process optimization across various industries, including automotive manufacturing, dredging operations, and paper mills. Employing cutting-edge technologies and digital tools has led to substantial improvements in:
- Efficiency
- Productivity
- Cost reduction
- Product quality
- Flexibility
- Environmental sustainability
This section explores the innovative solutions provided by the total systems approach and the Spectare® Intelligent Platform, as well as their use cases in an automobile shredder facility, dredging operation, and a paper mill.
Spectare® Intelligent Platform: Boosting Efficiency and Productivity
Industrial Service Solutions’ Spectare® Intelligent Platform has transformed efficiency and productivity in diverse industries by utilizing:
- Automation
- Advanced analytics
- AI-powered process control software
In an automobile shredder, for example, the platform integrates with existing equipment to optimize the shredding process, reducing energy consumption and increasing throughput. Additionally, the platform offers real-time data analysis and predictive maintenance to minimize downtime and enhance productivity.
Cost Reduction and Waste Minimization through Total Systems Approach
The total systems approach to performance monitoring has notably contributed to cost reduction and waste minimization in industries such as dredging by incorporating:
- Digital twins
- Simulation software
- Industrial Internet of Things (IIoT)
By integrating these solutions from the Spectare® Intelligent Platform into their operations, companies can effectively oversee and optimize their processes in real-time. Predictive maintenance helps decrease equipment failures and downtime, while the use of digital twins and simulation software enables virtual testing of processes. This leads to enhanced production efficiency, diminished waste, and lowered operational costs.
Improved Quality and Consistency with Spectare® Use Case
The total systems approach enhances product quality and consistency, as demonstrated by the Spectare® Intelligent Platform in a kiln operation at a paper mill implementing:
- Advanced process control software
- IIoT
- Machine vision systems
Spectare® ensures consistent temperature control and optimal energy consumption throughout the kiln operation, resulting in uniform product quality for the particular paper mill. This leads to higher customer satisfaction, fewer product recalls, and a strengthened market position and reputation for the organization.
Increased Flexibility and Adaptability through Total Systems Approach
The total systems approach to performance monitoring fosters flexibility and adaptability, vital for industries with fluctuating market demands with solutions such as:
- Cloud-based optimization platforms
- AI-driven analytics
- Industrial optimization algorithms
By using these technologies, the Spectare® Intelligent Platform empowers organizations to make quick decisions and adapt processes as needed. It enables organizations to respond to fluctuating market conditions, varying resource availability, and evolving regulatory requirements, ensuring efficient operations in a constantly changing environment.
Promoting Environmental Sustainability and Reduced Carbon Footprint with Spectare®
The total systems approach addresses environmental sustainability and carbon footprint reduction concerns across various industries, incorporating:
- Energy-efficient automation
- Waste reduction strategies
- AI-driven analytics
Employing this approach, the Spectare® Intelligent Platform reduces environmental impact and diminishes carbon footprints. This enables organizations to lower energy consumption, decrease waste generation, and optimize resource utilization, resulting in more sustainable manufacturing processes that safeguard the environment and its resources.
Competitive Advantage and Innovation through Total Systems Approach and Spectare®
In highly competitive industries, the total systems approach and the Spectare® Intelligent Platform facilitate innovation and competitive advantage by offering:
- Digital twins
- Simulation software
- Advanced analytics
These solutions enable organizations to virtually design and test new products and processes, accelerating product development and shortening time-to-market. This encourages a culture of innovation, allowing organizations to quickly iterate and refine their designs, ensuring they stay ahead of the curve and adapt to evolving industry requirements and customer needs.
Embracing the Future of Industrial Process Optimization
As we conclude our exploration of the industrial process optimization journey, it is clear that the importance of optimizing processes in the digital age cannot be overstated. Manufacturing and production facilities must continuously evolve and innovate to stay competitive and maintain operational excellence. With that in mind, let us reflect on the key takeaways from our discussion and consider the exciting future of industrial process optimization.
The Ongoing Importance of Industrial Process Optimization in the Digital Age
The digital transformation of industries has only intensified the need for effective process optimization. Advanced technologies, such as the Industrial Internet of Things (IIoT), artificial intelligence, and machine learning, have created new opportunities for organizations to fine-tune their operations and harness the power of data-driven decision-making. As we move further into the digital age, the pursuit of industrial process optimization will remain an essential factor in driving efficiency, profitability, and sustainable growth. Key aspects include:
- IIoT integration for real-time monitoring and data collection
- Adoption of artificial intelligence and machine learning for predictive analytics
- Data-driven decision-making for continuous improvement
Future Trends and Developments in Process Optimization Technology
The future of industrial process optimization promises exciting advancements in technology and methodology. Some key trends to watch include:
- Increasing integration of advanced analytics
- The rise of digital twins for virtual representation and testing
- Growing adoption of edge computing in industrial settings
These developments will further refine the optimization process, allowing businesses to stay ahead of the curve and capitalize on emerging opportunities for improvement.
The Impact of the ISS Spectare® Intelligent Platform in Revolutionizing Industrial Process Optimization
The ISS Spectare® Intelligent Platform and the adoption of a total systems approach to performance monitoring have the potential to revolutionize industrial process optimization. By offering real-time insights, predictive maintenance capabilities, and a comprehensive view of system performance, these cutting-edge solutions enable organizations to proactively manage their processes and drive continuous improvement. Key benefits of the ISS Spectare® Intelligent Platform include:
- Real-time performance monitoring and data collection
- Predictive maintenance capabilities for reduced downtime
- Comprehensive view of system performance for informed decision-making
As we embrace the future of industrial process optimization, the integration of such innovative platforms and methodologies will play a critical role in shaping the success of businesses and the industry at large.
The industrial process optimization journey has been a fascinating and transformative one, with ongoing relevance and importance in the digital age. By staying informed about future trends and developments in process optimization technology and harnessing the power of innovative solutions like the ISS Spectare® Intelligent Platform, businesses can unlock unprecedented efficiencies and propel themselves to new heights of success in the ever-evolving industrial landscape.